Asko washing machine errors
Asko brand automatic washing machines are able to independently detect breakdowns that have occurred in the system and notify users about them. If the control module notices that some part of the washing machine is not functioning correctly, the corresponding error code is immediately displayed on the display. All that remains is to open the instructions for the equipment and decipher the designation. This way it will become clear what failure occurred in the system and how to return the machine to functionality. Let's list the main error codes for Asco washing machines and look at what problems the equipment may indicate.
What errors does the Asco technique recognize?
The self-diagnosis system that modern washing machines are equipped with very often helps users out by helping to identify the cause of equipment failure. The explanation of all fault codes is given in the instructions for the washing machine. Asko. If you notice an error on the display, you should immediately look at the manual booklet.
On Asko models, the same errors can be indicated by different codes.
For example, to inform that the tank is not filling, on some Asko models there will be code E02, on others - F12. On the third, the phrase may simply be displayed: “Water supply fault”, in English – “Water inlet fault”. That's why it's so important to look at the instructions. For those who do not have the user manual, we will analyze the main fault codes recorded in the memory of Asco automatic washing machines.
- E01/Motor/Motor fault. The reason for the error display is a problem in the drive mechanism circuit. You will have to check whether the belt is in place, perform diagnostics on the engine, Hall sensor, reverse relay, and make sure that the wires in the area are not damaged.If it turns out that all of the listed elements are in order, all that remains is to inspect the control board.
- E02/F12/Water inlet fault/Inability to supply water. Appears on the display if the tank cannot be filled to the required level. First, you should make sure that the water supply in the house has not been turned off. See if the shut-off valve is open. During further diagnostics, be sure to pay attention to the inlet valve, inlet hose, mesh filter and pressure switch. Of course, a damaged control module could also be the cause.
- E03/F11/Draining fault. The code indicates that there is no drain. The pump cannot pump water out of the tank. In such a situation, it is worth checking whether the garbage filter, drain pipe or drain hose is clogged. It is also necessary to inspect the pump - it may have “burnt out” or become clogged with debris. The cause may also be a broken pressure switch that incorrectly determines the liquid level in the tank.
- E04 The error informs that water is supplied to the system slowly and in insufficient quantities. The code is displayed on the display if the tank is not filled to the mark within a certain time. Check whether the pressure in the water pipe is normal. If yes, clean the inlet hose, inlet filter and connections.
- E05 Appears when the water in the tank warms up more than necessary. The cause may be a faulty heating element, an incorrectly working thermostat, or a damaged circuit board.
- E06 This error, on the contrary, notifies that the water has not warmed up to the specified degree. You should also check the heating element, temperature sensor and wiring in the area. Lastly, the control module is inspected.
- Imbalance. It is displayed on the display when the drum is unbalanced, for example, when the laundry gets bunched up. It’s enough just to distribute things evenly in the machine.
- F10/Over Flow/Overfilling. The error informs about water overflow. In this case, you will have to check the inlet valve and pressure switch. If the pump does not start when the tank is full, it is also necessary to inspect it. Just as in other situations, the control module may be the culprit.
- Thermistor fault. Indicates that the temperature sensor is damaged. The thermistor will need to be replaced. If the wires come loose, just reconnect them.
- Pressure sensor error. Indicates problems with the pressure switch. It is necessary to diagnose the level sensor.
- Door lock fault. Informs that the door is not closed tightly. The hatch should be pressed against the body. If this does not help, test the UBL.
- Foaming. The “brain” stops the wash due to a large amount of foam in the tank. To eliminate the error, you should run a rinse cycle, and in the future do not exceed the dosage of detergent.
If the Asko washing machine is still under warranty, you should not try to repair the equipment yourself. It is better to immediately call the service center and invite a specialist for free diagnostics and repairs.
Tips for troubleshooting
By deciphering the fault code displayed on the display, you can decide whether it is realistic to carry out the repair yourself or whether you will have to invite a specialist. There is nothing difficult about cleaning the elements of the drain system from blockages, replacing the pressure switch or heating element, and tightening the drive belt. Asko washing machines have typical faults. Let's figure out what kind of breakdowns owners of equipment of this brand most often encounter, and give recommendations that will help you repair the machine yourself.
- The inlet valve has failed. This part regulates the flow of water into the tank.When the device breaks down, the machine cannot be filled, or, on the contrary, too much liquid is filled. To get to the solenoid valve, you only need to remove the top panel of the housing. The sensor cannot be repaired; you will have to replace it with a new one.
- The inlet filter is clogged. This is a mesh installed at the connection point of the inlet hose, in front of the inlet valve. You need to pull out the filter element with pliers, then clean and rinse it and then put it back.
- The pressure switch is faulty. It is also located just under the top cover of the case. To check the device, you need to disconnect the tube from the level sensor and blow into it. If you hear clicks, it means the element is working. “Silence” will indicate that the pressure switch has failed. Diagnostics is also performed using a multimeter. A “burnt out” part cannot be repaired; only replacing it will help.
- UBL is not functioning. In such a situation, the machine door does not lock, and the machine cannot start washing, since the system is not airtight. You can try to repair the locking mechanism or immediately install a new device.
- The heating element has failed. Scale accumulating on the surface of the element disrupts its thermal conductivity. It overheats and burns out. Replacing the tubular heater is very simple; you need to remove the back wall of the housing and find the heating element (Asko has it in a non-standard place - on the side of the tank). Then you need to remove all the supply wiring from it, loosen the nut and remove the part. Next, a serviceable spare part is put in place.
- The thermostat stopped working. The temperature sensor is located on the heating element; you can also check it with a multimeter. The thermistor cannot be repaired; the part will need to be replaced.
In most cases, you can fix the “home assistant” yourself.
The main thing is to strictly follow the instructions for action and observe safety regulations. Difficulties may arise with more serious repairs, such as replacing bearings. It is better to trust diagnostics of the control module only to specialists; it is not recommended to “dig” into the electronics yourself.
Interesting:
Reader comments
- Share your opinion - leave a comment
Categories
Washing machine repair
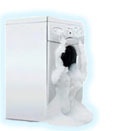
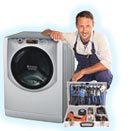
For buyers
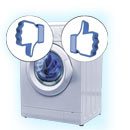
For users
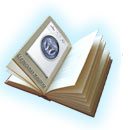
Dishwasher
Add a comment