Damage to Daewoo washing machines
Automatic washing machines from the Korean manufacturer are distinguished by their reliability and high build quality. However, they, like any other machines, are not immune to breakdowns. Let's figure out what malfunctions of the Daewoo washing machine users encounter most often. We'll tell you how you can fix the equipment yourself.
Most common defects
Before buying an automatic machine, people try to find out about the most vulnerable points of each brand’s equipment. If we talk about Daewoo washing machines, they do not have any obvious weaknesses. The breakdowns that Daewoo users encounter are quite typical:
- failure of the pressure switch;
- clogging of the inlet mesh filter;
- Thermistor malfunction. With such a failure, the water does not warm up well, the machine may “freeze” during the washing process;
- drive belt wear. The problem may appear after several years of using the machine. If the rubber band has worn out within literally six months of use, there is most likely a manufacturing defect;
- problems with the heating element. Usually, problems with the heater are caused by too hard water and insufficient care of the equipment. So, scale forms on the element, and because of this deposit the part may burn out;
- hatch cuff defect. In most cases, the seal deteriorates due to the user’s violation of the rules for operating the washing machine;
- failure of the control board.
In addition, the weak point of Daewoo automatic machines is the drum. Over the years, it can rust from too hard water. To prevent this, it is important to install a softener filter at the entrance to the washing machine.
The listed malfunctions are typical for both frontal and horizontal Daewoo vehicles.
It is not necessary to invite a specialist to repair a “home assistant”. Most problems can be fixed with your own hands. We'll tell you what to do in each specific case.
Drive mechanism problems
Owners of Daewoo washing machines sometimes encounter the problem of a non-rotating drum. The machine does not start washing because the centrifuge freezes. The reason for this may be wear on the commutator brushes, breakdown of the engine winding, failure of the tachogenerator, or breakage of the drive belt. If any of the above malfunctions occur, normal operation of the unit will be impossible.
To check the elements of the drive system, you will have to remove the rear wall of the case. Having opened access to the parts, you should begin diagnosing the components. Inspect the drive belt. If it is not on the pulley, it means it is under the machine. A loose rubber band usually becomes very stretched and needs to be replaced. The cause of a broken belt may be:
- low quality gum;
- natural wear and tear of the strap;
- constant overload of the machine with things, which causes the drum to scroll;
- loosening of the pulley;
- factory defect of the drum “wheel”.
To check the motor and Hall sensor, remove the motor from the housing. To do this, you will need to unscrew the two bolts holding it. First, inspect the commutator brushes - if the graphite rods are ground off by more than 50%, they will need to be replaced (be sure to change both electric brushes, even if one of them is intact). To test the tachogenerator, you will need a multimeter. The same device will be needed to diagnose the stator and rotor windings of the engine.
The system is clogged
Often Daewoo washing machines stop working normally due to blockages in the system. In this case, it is very easy to return the machine to “life” with your own hands, without resorting to the help of a specialist.
A slow or non-existent drain of water from the tank will indicate a blockage.
A blockage can form in the following places:
- garbage filter. Most often, dirt accumulates here;
- pump. The pump on Daewoo cars rarely gets clogged, since an additional filter element is installed in front of it;
- drain pipe. It connects the pump to the tank;
- drain hose. This is a corrugation through which water flows directly into the sewer.
What to do in such a situation? The first thing you should check is the garbage filter. For Daewoo washing machines it is “hidden” behind the lower false panel. Before unscrewing the cap, cover the floor around the machine with dry rags and prepare a low container. Water will pour out of the hole, so you need to be fully prepared.
Having unscrewed the “trash can”, inspect it. Remove all debris from the spiral, shine it into the “socket” where the filter is inserted. Remove objects stuck in the hole and clean dirt from the walls. After this, put the “plug” back. Then you should inspect the drain hose. Feel the corrugation. Having noticed the seal, disconnect the sleeve and clean it with a special brush. Then put the drain back in place.
Next, you can disassemble the machine and clean the drain pipe and pump. To get the pump, you need to remove the wiring from it and unscrew a couple of bolts. To remove the pipe, you will have to loosen the clamps securing it. If the elements of the washing machine's drainage system are in perfect order, but the water still does not want to leave the tank, it may be a clogged sewer. To eliminate the cause, you will have to call a plumber.
Inlet valve, filter element, pump
A failed solenoid valve cannot be confused with any other malfunction of a Daewoo washing machine. If the inlet membrane does not function correctly, water will either not flow into the tank, or, on the contrary, will flow into the system by gravity, even when the machine is disconnected from the power supply.
If you notice the “murmur” of water being drawn in and drained when the washing machine is turned off, urgently check the inlet valve.
First you need to remove the top panel of the Daewoo machine by unscrewing the two bolts holding the cover. The solenoid valve is located at the point where the inlet hose is connected to the washing machine body. Next you need to check the valve gaskets. If they are not deformed, test the part with a multimeter. If the resistance at the contacts of the intake sensor is within 30-50 Ohms, it means it is working. If you find that the fill valve is broken, you should replace it; the element cannot be repaired. You need to buy a part, unscrew the faulty sensor from the machine and install a new one, connecting all the pipes and wires to it.
If you notice that the Daewoo washing machine does not drain water and you cannot hear the sound characteristic of a running pump, you should check the pump. To gain access to the part, you will have to lay the washer on its side and remove the element through the bottom. Next, you need to inspect the pump impeller, remove hair and other debris from the part. Afterwards, the element body is disassembled and all dirt is cleaned from the inside. The pump should also be tested with a multimeter to prevent the unit from “burning out.”
All of the “symptoms” described above may be the result of problems with the electronic unit. If the triacs or tracks on the board are damaged, the operation of the washing machine will be disrupted. Diagnostics and repair of the control module should be entrusted to professionals. Digging into the “brain” of a machine with your own hands is dangerous - you can harm the equipment even more.
Self-diagnosis system codes
Modern washing machines are able to independently detect breakdowns that have occurred in the system and notify users about them. Machines equipped with a display display the corresponding error code on the display, units without a screen notify of problems by flashing the display.
The explanation of error codes is given in the instructions for the Daewoo washing machine.
If you notice that the washing machine has frozen and displayed an error on the display, you should immediately open the user manual. The self-diagnosis system allows you to narrow the range of possible breakdowns and speed up the search for the cause of the malfunction. Let's figure out what this or that code indicates.
- OE error. Informs that the Daewoo washing machine cannot remove water from the tank. You will have to check all the elements of the drain system one by one. For starters, a garbage filter and a drainage hose. Then you should inspect the pump, pipes, and make sure that the wiring in the “pump-control module” section is not damaged.
- IE code. Indicates that water is not being added to the system or is very slow. This error does not always indicate a breakdown. Perhaps the water supply in your home was turned off or its pressure was reduced. The shut-off valve is also likely closed. If everything is in order with the water supply and the tap is fully open, you will have to check the inlet valve of the washer, the filter mesh, and inspect the inlet hose.
- UE error. Indicates that the drum is unbalanced. Usually occurs when laundry gets bunched up in the washing machine. That's why it's so important to distribute things inside evenly.In addition, the code may appear if the machine is not installed level. An even rarer cause is damage to the counterweight unit.
- Code LE. The machine gives an error without starting the wash. The designation indicates that the drum door is not tightly closed or the hatch locking device is faulty.
- Error E This symbol notifies you that the loading sensor has failed. In such a situation, the Daewoo machine does not start working and does not begin to rotate the drum. The element will have to be replaced.
- Code E Indicates problems with the pressure switch. You will have to check the level sensor and make sure the connections are intact. If the element itself is broken, it will need to be replaced; the part cannot be repaired.
- Error H Informs that the water is not heated to the set temperature. It may indicate either a break in the heater circuit or a failure of the heating element itself. If the reason is a damaged element, you will have to replace it.
If you notice that your Daewoo machine has stopped working, do not panic. If the washer is still under warranty, it is better to call the service center, in which case diagnostics will be free. When the warranty period has long expired, you can “dig” into the device with your own hands, find out the cause of the malfunction and fix the “home assistant”.
Interesting:
Reader comments
- Share your opinion - leave a comment
Categories
Washing machine repair
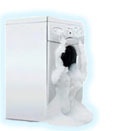
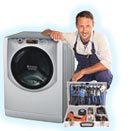
For buyers
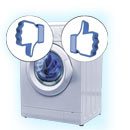
For users
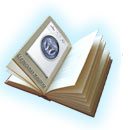
Dishwasher
Add a comment