DIY washing machine motor repair
The washing machine engine is the heart of the unit, the most important organ, without which all the others will not work. Of course, when an engine burns out, you need to fix the problem as quickly as possible, but buying a new part can be quite expensive. Actually, like buying a new car. But what if you can repair the washing machine engine and thereby give it a second life? Let's see if this is possible, and if so, how?
First, the “engine” needs to be removed
There are three types of SM motors: inverter, commutator and asynchronous. At the moment, most washing machines around the world are equipped with commutator motors, so using their example we will consider the entire procedure.
Naturally, you need to start by disassembling the washing machine and removing the engine itself. Disconnect your home assistant from all communications and position her in such a way that you have easy access to her from all four sides. Take action.
- Remove the panel hiding the utility lines. For front-loading machines, this is the rear panel; for vertical-loading machines, it is the side panel. Unscrew the bolts and slide the wall down.
- Locate the pulley (the large wheel adjacent to the drum) and the drive belt that goes onto it. Grasp the belt at this point, rotate the pulley and remove the belt. The algorithm of actions is reminiscent of replacing a bicycle chain.
- Remove the wiring from the motor.
- Using a spanner wrench or other suitable tool, remove the screws holding the motor in the socket.
- Take out the engine.It is held on by straight pins, so you need to take it out by rocking it slightly down and forward. Experienced craftsmen lightly tap with a hammer to make the task easier, but it’s better not to take risks, you don’t want to inadvertently damage the part.
Usually the dismantling process is easy for users. Now that the electric motor is in your hands and before your eyes, you can begin diagnostics.
Test run of the removed engine
It is necessary to start the engine in test mode. To do this, find a 220-volt AC source. Connect the rotor and stator windings into a series circuit, and connect the AC source to the remaining connectors.
Important! To insure yourself in case of a short circuit in the motor, you must also connect an electrical device with a power of approximately 500 Watts into the circuit; a heating element of a washing machine or some powerful lamp will do; if a short circuit does occur, the heating element will begin to quickly warm up, and the lamp will burn brightly .
You will be very lucky if you find a powerful automotive transformer, with a power above 500 watts, with its help it is very good to power the circuit. The speed of the existing engine will be easier to control. Fuses with a current rating of 5-10 Amps can be included in the circuit for greater safety.
When the engine begins to rotate and picks up speed, look for strong sparking where the brushes and commutator meet. If it sparks strongly, the motor is most likely faulty. In general, brushes, commutator lamellas, as well as rotor and stator windings are the most vulnerable parts of the motor, which most often fail.
Checking engine elements with a tester
If the cause of the malfunction lies in the rotor or stator winding, this can be identified by the specifics of the engine’s operation: the power is rather weak, extraneous noise appears, and during a test run it gets very hot. A multimeter will help you check this guess. It must be configured to measure resistance. Now do the following:
- find the engine passport, where reference measurement values are given. Next, successively apply the multimeter probes to the rotor lamellas. Differences in values should not be more than 0.5 Ohm, and the values themselves should correspond to the reference values. If there is a deviation, there is an interturn short circuit;
- if you don’t have a passport, you can try a tactile and charming way to determine the problem. If the resistance in the lamellas is insufficient, the current strength increases, which leads to heating of the lamellas, you will feel it with your fingers. At the same time, a characteristic burnt smell will appear;
- if the resistance, on the contrary, goes off scale during dialing, this indicates a break in one of the windings;
- Now, using the same scheme, you need to ring the motor stator. Perform resistance measurements between the winding contacts;
- Now you need to check the short circuit of the windings to the stator housing. Apply one multimeter probe to the iron part of the stator, and the other to all slip rings in turn.
If the stator operates without interruption, the resistance value will be very high, most likely reaching hundreds of Mega Ohms.
Are the slats intact?
The rotor lamellas are held on to it by a special adhesive material. When the rotor jams, or a short circuit occurs between the turns, strong heating occurs and the lamellas begin to peel off. It is also possible that the contact in the rotor section has broken.
Sometimes small nicks appear on the lamellas, which cause the brushes to wear out faster and spark heavily. The reasons for such a breakdown may be jamming of the rotor or starting the wash with the drum flaps open in machines with a vertical loading type.
Are the brushes intact?
The brushes are part of the motor, so for diagnostics they need to be removed from there. Let's look at the algorithm using the example of a Bosch top-loading washing machine. Bosch manufacturers use standard commutator motors in all their models, so the information described below will be relevant for the vast majority of owners of washing machines.
- Remove the engine and place it so that it is convenient to work with it.
- In older motor models, the brushes were located under the top cover, so you had to remove the motor to get to them. If your engine is of this type, mark with something the location of the fixing screws on the housing and stator before disassembling them. You can use a bright marker or scratch the marks with something sharp.
If you mix up the sides during subsequent assembly, just starting the car, you will be faced with the fact that the tachogenerator coil will burn out. The tachogenerator is responsible for the engine speed, and the coil itself is wound on a wire as thick as a hair. If there is an error, voltage will be supplied not to the brushes, but to the coil, which will lead to burnout.
Note! Of course, you can return the stator coil to its place, but you won’t be able to just regulate the engine speed, even though the engine itself will work quite well.
- In modern engines, brushes can be removed without disassembly. Find the side of the motor opposite the shaft.There you will see special pads, each with one wire connected to it. To remove the brush, remove the terminal from the pad by prying it with something sharp.
- On the site you will see two small niches. Move the pad to the left so that the notches align with the metal sides that hold the brush.
- Use something to hook the brush and take it out.
Now take a close look at the product. New brushes are about 35 millimeters in length, and those that have been in use for a long time are 5-10 millimeters. Based on this information, determine whether your brush is still fit for service.
Troubleshooting Engine Problems
All the problems described above are quite easy to repair with your own hands. In the guide below we'll take you from simple to complex, starting with brushes.
There is no point in describing the installation process in detail, since it is intuitive. As a last resort, repeat the steps described above in reverse order. However, as for the details themselves, a few words should still be said about them.
Almost all brushes produced in factories are glued, and few people manage to find original spare parts in retail stores.
But there are a dime a dozen solid elements from third-party manufacturers on store shelves, and this puzzles ordinary users. Moreover, on the Internet, some masters are actively persuading the use of glued brushes because of their softness, but it is simply not possible to verify in practice whether this is true or not, so you should not be puzzled: take what you find.
The next most difficult repair is the rotor lamellas. If the problem is advanced and the detachment of the lamellas is too severe, the rotor cannot be repaired.But if the lamellas have peeled off by only +- 0.5 mm, then a turning groove will help.
- Fix the rotor well on the machine.
- Start the machine.
- Align the thickness.
- When the procedure is completed, it is necessary to perfectly clean the gaps between the slats so that not a speck remains there.
- Next, test the resistance of the lamellas with a multimeter. If the short circuit still persists, repeat the stripping procedure until it is completely eliminated.
Attention! This method of repair is short-lived, since it eliminates the consequence of the problem, and not the problem itself and not its cause; a repaired old one will definitely not work better than a new factory manifold.
What should those whose lamellas have peeled off by more than 0.5 mm or come off completely? Feel free to get rid of the old rotor. It is practically beyond repair. In rare cases, something can be done, but you can’t do it without special expensive equipment. As for the stator and rotor windings, repairs are again possible, but this is not economically feasible. You can’t do it with your own hands; you need to look for a person who will agree to rewind the winding, but he will charge such a price for it that it is easier to buy a new motor and even pay a technician for installation.
Interesting:
Reader comments
- Share your opinion - leave a comment
Categories
Washing machine repair
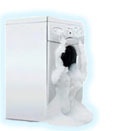
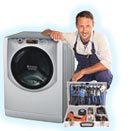
For buyers
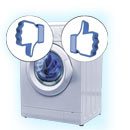
For users
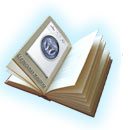
Dishwasher
Add a comment