Kandy's washing machine constantly fills with water
If the Candy washing machine constantly fills with water without starting to wash, then there is a failure in the system. It will not be possible to ignore such a problem - the machine simply will not be able to continue to perform its functions. Let's figure out what could be the reasons for the continuous accumulation of fluid, what to do in this situation.
Signs of a problem
With a standard cycle, the Kandy machine fills the tank about four times. During the main wash and when rinsing clothes. It is quite easy to understand that liquid enters the tank continuously. The following “symptoms” will indicate that the machine has problems with water intake:
- the constantly present noise of liquid being poured into the tank;
- extended cycle. Since the machine does not function correctly, the program execution time is extended;
- dirty and soapy things in the drum. Due to the fact that the required concentration of soap solution is not achieved, the laundry cannot be washed properly.
Having noticed that the usual program has become longer by 30-40 minutes, observe the operation of the washing machine. Start the mode and see if there are any problems with water intake. The same applies to the situation if after washing there is a lot of powder and soap stains left on things.
It is dangerous to operate a washing machine that has problems with water supply.
Potential culprits
The reasons that the Kandy automatic machine constantly takes in water can be different. First, it is necessary to analyze all possible factors, and during the diagnosis, eliminate one by one. Continuous fluid intake can be caused by:
- a hole in the tank of the car;
- broken water level sensor;
- incorrectly functioning intake valve;
- damaged control module.
It is important to check each of the elements. Very often, a continuous supply of water is observed when the machine is incorrectly connected to the house communications. Some breakdowns can be dealt with with your own hands; for complex repairs you will have to invite a specialist. We'll tell you what to do if a particular malfunction is detected.
Incorrect installation of drain hose
Diagnostics of household appliances is always carried out from simple to complex. Therefore, experts recommend first checking whether the machine is correctly connected to the sewer. An incorrectly positioned drain hose may well be the cause of the breakdown.
The washing machine always comes with instructions that spell out the basic rules regarding the installation of the equipment. It even shows how to connect hoses to house communications. Unfortunately, many users do not pay attention to the manufacturer's recommendations and organize the output points incorrectly.
The drain hose must be at a level of 50-60 cm from the floor, otherwise the water will flow out of the tank by gravity.
If the drain hose is “run” along the floor, the water drawn into the machine will spontaneously flow out of the system. The pressure switch, recognizing that the tank is empty, will transmit a signal to the board, and the control unit will again “order” the inlet valve to fill the washing machine. This process can continue in circles for a very long time.
Therefore, first of all, inspect the drainage hose, make sure that it is located at a sufficient distance from the floor. If you cannot visually check the sleeve, you can do this in another way:
- turn on the equipment;
- activate any washing mode;
- wait until the washer fills with water;
- click on “Pause”, move the selector to the “Drain” mode;
- run the function;
- in the middle of the “descent”, pause the cycle.
If water still gradually pours out of the tank after stopping the process, then the reason is definitely in the drainage hose. If the fluid level does not change, you need to think further.
Fill valve does not hold
In some cases, persistent flooding is due to a faulty inlet valve. Such a sensor cannot stop the flow of water into the system. When the washing machine is filled to capacity, the protection is triggered and the drain is activated. What should I do to return the machine to functionality?
First, observe the technology. If water is poured in too slowly, it is most likely due to a worn out membrane. Rapid filling of the tank indicates a malfunction of the electromagnetic sensor itself. The inlet valve cannot be repaired and will need to be replaced.
Having purchased a new part that is suitable specifically for your Kandy model, you can begin replacing the valve. For this:
- turn off the power to the washing machine;
- remove the top cover of the housing on a front washing machine, or the side cover on a “vertical” washing machine;
- find the fill valve;
- take a photograph of the diagram for connecting the wires and pipes to the sensor;
- disconnect the wiring and tubes from the element;
- remove the old valve. Depending on the model of the automatic machine, you will need to either unscrew the bolts holding the part, or loosen the latches;
- put the working part in place. Secure it with latches or screws;
- connect the previously reset wiring, connect the pipes;
- assemble the body.
To check whether the replacement was carried out correctly, run a “idle” wash with an empty drum.See if the problem has been resolved. It is not difficult to dismantle the old valve and install a new one; all this is done with your own hands, without contacting a specialist.
Pressostat
The level sensor monitors the amount of water in the tank. When the desired mark is reached, the pressure switch signals the “brain” of the machine. The control module, in turn, “orders” the liquid intake to be completed.
If the pressure switch breaks down, the electronic module receives false information about the water level in the machine.
Because of such “turmoil,” the entire process is disrupted. Incorrect operation of the sensor may be caused by:
- oxidation of its elements;
- short circuit of wires;
- damage to the fitting;
- clogging;
- depressurization of the membrane.
There are several ways to troubleshoot the problem. First try to fix the pressure switch. Perhaps cleaning contacts, removing blockages, and “welding” defects will help. If there is no return, you will have to install a new level sensor.
The sequence of actions is as follows:
- remove the top panel of the case by unscrewing the bolts securing it;
- “unhook” the pressure tube from the pressure switch;
- reset the chip with wires;
- pull out the level sensor by releasing the fasteners;
- reinstall the working part;
- connect the tube and wiring to the new pressure switch;
- Secure the cover of the machine with self-tapping screws.
When repairing equipment yourself, you must follow safety regulations. Before starting work, be sure to unplug the machine’s power cord from the outlet and turn off the water supply tap.
It is important to purchase original components. The pressure switch must correspond specifically to the specific model of the washing machine.
Electronic filling
If the diagnostics of all the described sensors and elements did not reveal any problems, all that remains is to check the main control unit. The electronic module completely controls the washing process; if it is damaged, the cycle may be disrupted.
If any element of the control board is damaged, the “brain” cannot correctly recognize and transmit signals. So, for example, the pressure switch notifies that the tank is full, the module does not respond, the protective system drains the water, and the liquid intake continues.
The reasons for damage to the electronic module may be the following:
- power surges;
- moisture getting on the board;
- element wear;
- a defect resulting from mechanical impact on a block.
If the control module fails, there is no point in trying to repair it. To “dig” into electronics, you need appropriate knowledge and skills. An inexperienced person getting into the “brain” of the washing machine can only worsen the situation.
Interesting:
Reader comments
- Share your opinion - leave a comment
Categories
Washing machine repair
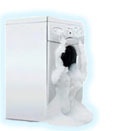
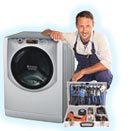
For buyers
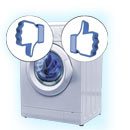
For users
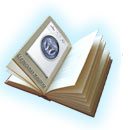
Dishwasher
Add a comment